Nalco Water Heat Optimized Maintenance Cost and Improved Reliability for a Petrochemical Plant
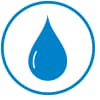
The Situation
A North American petrochemical plant routinely cleaned a large number of water cooled heat exchangers each year as part of the normal maintenance practice. The plant had no metrics or performance data available to make precise heat exchanger performance evaluations. Without sufficient data to determine whether an exchanger needed to be cleaned, numerous exchangers were cleaned unnecessarily.
"By the 5th year of implementing HEAT, heat exchanger cleaning costs had been reduced by 80% annually - $600,000 in physical cleaning cost savings alone."
The Solution
Working closely with the customer's operations team on managing heat exchanger reliability, a team of technicians and engineering consultants conducted a comprehensive cooling system audit, collecting and processing flow, temperature, inspection, and mechanical data and analyzed it in HEAT's digital platform. Based on the findings, rectifying actions were taken, the heat exchanger maintenance schedule was optimized, and the plant agreed to keep HEAT as a routine service.
The Results
As a result of the rectifying actions and improved heat exchanger monitoring, Nalco Water was able to remove unnecessary cleanings from the spring-cleaning list. By year five, total heat exchangers cleaned per year were reduced from 35 to 7 while maintaining unit performance and reliability.
This comes down to an 80% reduction in cleaning costs which translates into approximately $600,000 USD in cleaning costs savings per year.